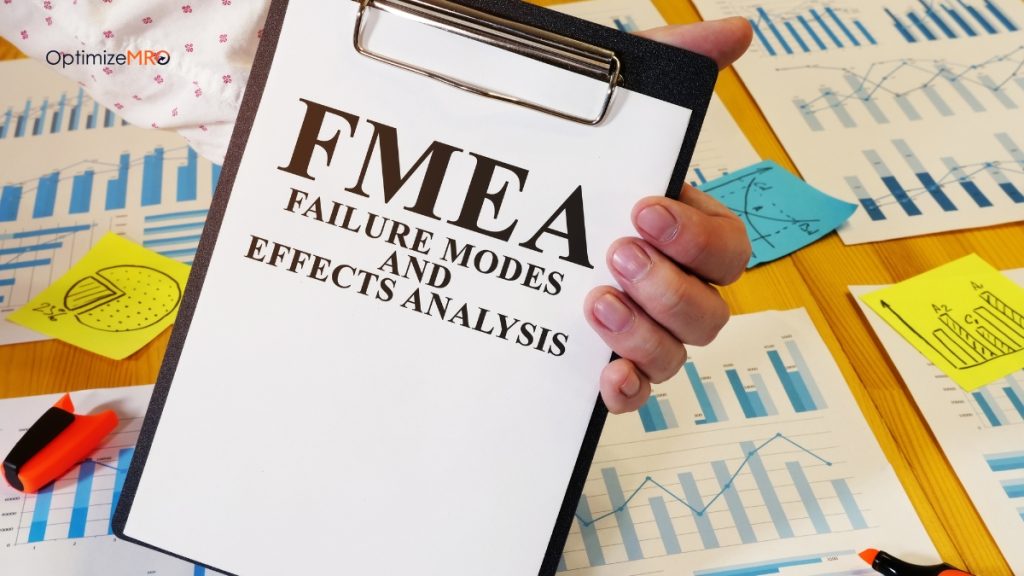
- Severity (S): This measures the seriousness of the consequences if a particular failure occurs.
- Occurrence (O): This evaluates the likelihood that a specific failure mode will happen.
- Detection (D): This assesses how effectively existing processes or controls can detect a failure mode before it impacts the end user.
- Process Review: The first step in the FMEA process is identifying the specific task or procedure where potential failures, their causes, and their effects will be assessed.
- Identifying Failure Modes: Next, potential failure modes for the equipment or process are identified. These represent the ways in which the product, system, or process could fail to perform as intended.
- Calculating SOD Scores: Each failure mode is then analyzed to determine how it could affect the system or process. This involves assessing the severity, likelihood of occurrence, and the effectiveness of existing controls to detect the failure before it impacts the end user.
- Assigning RPN: The RPN score helps prioritize risks, with failure modes ranked based on their Severity, Occurrence, and Detection scores, allowing organizations to focus on the most critical risks first.
- Implementing Mitigation Strategies: Based on the risk assessment, strategies are then developed and implemented to address the most pressing issues. This may involve changes to the process, product, or service, as well as adding new controls or monitoring systems.
- Monitoring and Review: FMEA is not a one-time process but rather an ongoing activity. Organizations should regularly monitor and reassess risks to ensure that the mitigation strategies remain effective and relevant over time.
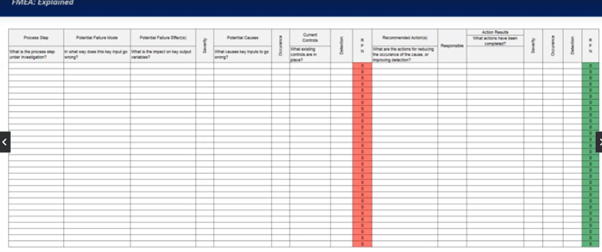