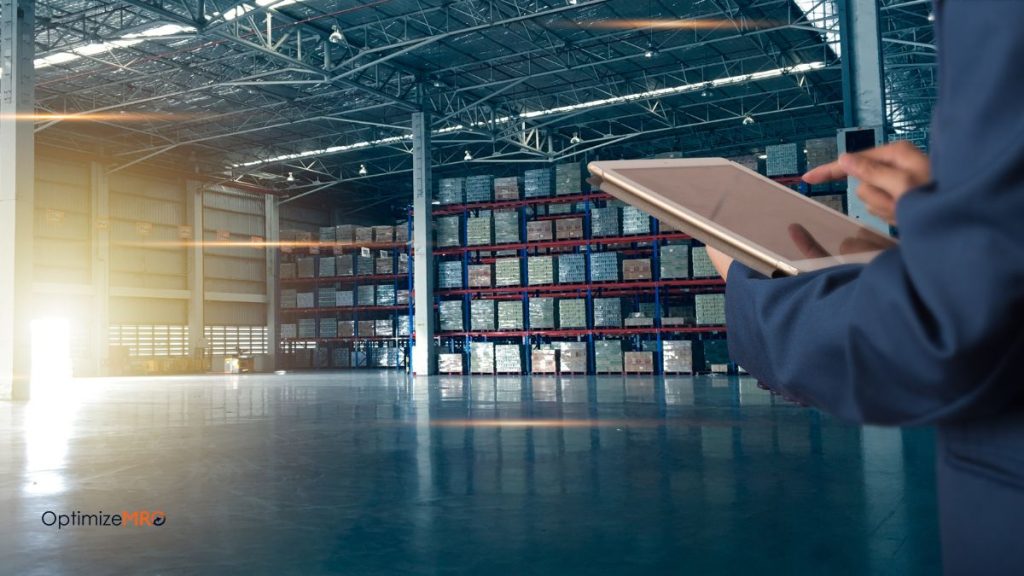
Unwanted stocks in inventory refer to excess or duplicate items that a company holds, which could include raw materials, consumables, spares, work-in-progress, semi-finished goods, or finished goods that are no longer needed or are unlikely to be sold. Unwanted inventory ties up capital and consumes storage space, which can be costly for a business.
Here are some common reasons why inventory might become unwanted:
- Overproduction: Sometimes industries produce more goods than there is demand for, leading to excess inventory.
- Change in Demand: Shifts in consumer preferences or market trends can render certain products obsolete, resulting in unwanted inventory.
- Obsolete Products: Technological advancements or changes in product lines can make certain items obsolete.
- Human Errors: Mistakes in creating and purchasing items can lead to duplicate or unnecessary stocks, as items already available are not utilized over time.
To address these issues, it is crucial to count and gather all information related to unwanted stocks. Analyzing areas with significant deviations can help in developing proper solutions.
To mitigate these errors, follow these steps:
- Check Existing Inventory : Engineers or technicians must check the ERP system for existing materials before making a purchase. If unsure whether an available item meets their needs, they should consult the previous purchaser. If the item matches their requirements, they can use the same code and raise a PR; if it differs, they need to create a new one.
- Improve Descriptions: If the existing item is the same but poorly described, they should seek permission from the responsible purchaser to update the description, ensuring future users are not misled.
- Avoid Free Text : Users often misuse free text to specify requirements, leading to multiple purchases under the same material code. For instance, a description like “PAINT, GLOSSY, ENAMEL, SPRAY, LEAD-FREE” can lead to different items being purchased based on color specifications added in free text. Blocking free text can prevent such misuse.
- Hire Data Governance Professionals : Employ a data supervisor or data governance officer to manage new material code creations and correct old data errors in the ERP system.
- Develop a Governance Tool : Implement a proper governance tool with high-level approval and monitoring processes. This ensures only standard data is created and maintained in the ERP system.
- Mindful Purchasing : Purchasers should be diligent when approving and creating purchase orders. If mandatory values are missing from descriptions, they should notify the data governance professional to make necessary changes.
- Monitor Inventory Consistency : Storekeepers or in-charge personnel should monitor the same category of items received from different departments. If items are identical but purchased under different material codes, they should advise the authorized person to consolidate the stocks under a single code and block the other codes for future purchases.
Before implementing these tasks, ensure that existing data is clean, consistent, and standardized with well-arranged descriptions. This will help create error-free and duplicate-free data. Optimize MRO specializes in inventory data management, providing services related to inventory management. We assist in cleaning and enhancing your data to industrial standards using our highly specialized data cleansing experts.