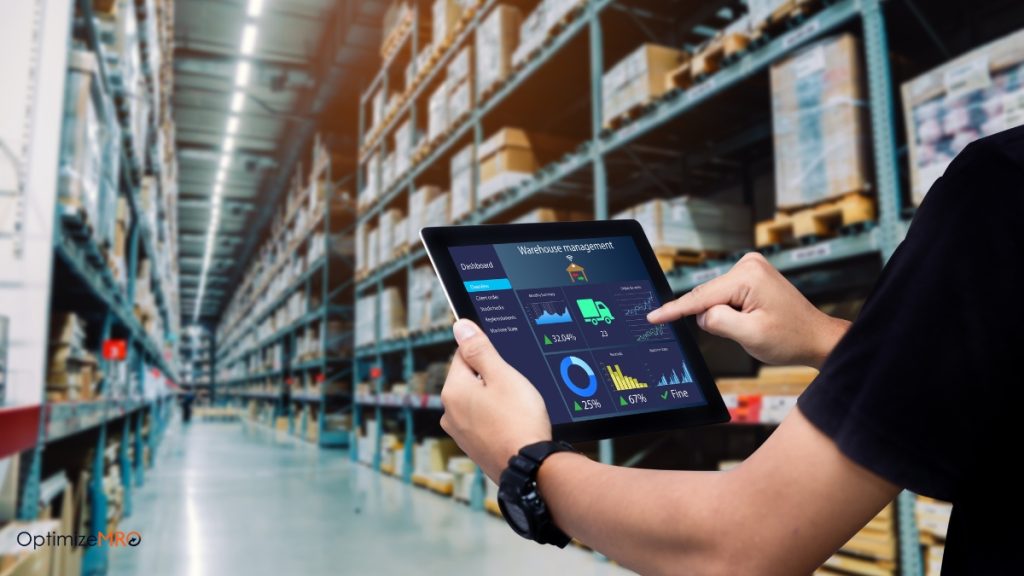
Modifying material groups in an organization’s inventory and spend analysis system is a comprehensive measure. Material groups play a vital role in categorizing products for ERP systems, making them essential for procurement, inventory, and financial management.
Let’s delve into how changes in material groups can influence inventory control and spend analysis.
1. Spend Analysis
Spend analysis involves examining and categorizing business expenditures to identify patterns, cost-saving opportunities, and improve purchasing strategies.
Category Visibility: Material groups often form the basis of spend categorization. Altering a material group can affect how purchases are grouped in reports, potentially revealing or obscuring significant cost-saving opportunities.
- Impact: Moving an item between groups (e.g., from “Office Supplies” to “IT Equipment”) can change the cost distribution of a category, affecting the accuracy of spend analysis and historical comparisons.
Supplier Insights: Spend analysis also tracks supplier performance across material groups. Changing categories may disrupt prior analyses of supplier pricing, necessitating updates or reclassification to maintain consistency.
- Impact: Frequent changes to material groups can make it challenging for procurement teams to assess supplier performance over time, complicating the tracking of trends like pricing fluctuations or delivery reliability.
Budgeting and Forecasting: Material group structures inform budget allocations and future planning. Changes in these structures can misalign budgets with actual needs.
- Impact: Inconsistent budget allocations due to material group changes can hinder accurate forecasting, requiring adjustments to procurement strategies and budget planning.
2. Inventory Management
Effective inventory management aims to meet demand at minimal cost while keeping holding costs low.
Inventory Tracking & Classification: Inventory management focuses on meeting demand efficiently while controlling holding costs. A material group change that reclassifies a “Finished Good” as a “Raw Material” can affect stock management strategies, reorder levels, and stock balances.
- Impact: Incorrectly managed changes may lead to extended restocking times or discrepancies in stock records.
Stock Optimization: Inventory systems like just-in-time (JIT) depend on accurate material grouping. Changes can alter optimization parameters.
- Impact: Reclassifying an item from a raw material to a finished good may require higher minimum stock levels or new rotation strategies. Mismanagement could lead to overstocking, understocking, or inefficiencies in inventory control.
Demand Planning and Replenishment: Automated systems forecast demand based on material groups. Changes can disrupt these forecasts, leading to surplus inventory or deadstock.
- Impact: If demand forecasts fail to align with reorder points due to material group shifts, stockouts or excess inventory may occur.
Costing and Pricing: Different material groups often use distinct costing methods, such as standard costing or moving average. Reclassification can affect inventory costing models, impacting cost of goods sold (COGS) and overall financial reporting.
- Impact: Changes in material group classification may affect inventory carrying costs, profit margins, and accounting accuracy.
3. Other Implications :
System Integration and Data Quality: ERP systems link data across finance, inventory, and procurement. Material group changes may necessitate significant system updates to maintain data integrity.
- Impact: Adjusting material groups in ERP systems requires careful data integration to ensure consistency across departments.
Process and Workflow Adjustments: Departments such as finance, procurement, and inventory management may need to revise workflows and retrain staff to adapt to reclassified material groups.
- Impact: Poorly managed changes can disrupt workflows, necessitating updates to performance metrics and employee training.
Best Practices for Managing Material Group Changes
- Clear Documentation and Communication: Ensure all stakeholders (procurement, inventory management, finance, etc.) understand the reasons and implications of changes.
- Update Systems: Revise ERP systems and analytics tools to reflect new material groupings, including historical data adjustments for consistency.
- Revisit Procurement Strategies: Review sourcing strategies and supplier contracts to account for reclassification impacts on supplier performance and pricing.
- Monitor Key Metrics: Track KPIs like inventory turnover, stockouts, supplier performance, and cost trends to identify and address issues arising from reclassification.
Changing material groups impacts spend analysis, inventory management, and financial accuracy, requiring careful coordination and integration. OptimizeMRO simplifies this process with expert solutions in inventory optimization, spend analysis, and ERP integration. We ensure smooth transitions, minimize disruptions, and maximize efficiency, helping your business achieve cost savings and operational excellence.